In Japan, a country renowned for its precision engineering and advanced manufacturing, companies like Hitachi and Toshiba are utilizing artificial intelligence (AI) to innovate predictive maintenance. This application of AI is a game-changer for the manufacturing industry, offering the ability to predict equipment failures before they occur, thereby minimizing downtime and extending the lifespan of machinery. AI algorithms analyze data from sensors embedded in machinery, learning from historical operation patterns to predict future breakdowns with significant accuracy. The benefits of this technology are manifold.
Firstly, it allows for substantial cost savings by reducing unplanned maintenance and extending the intervals between repairs. Secondly, it enhances production efficiency by ensuring machinery operates at peak performance without unexpected interruptions. Additionally, predictive maintenance supports Japan’s environmental goals by optimizing the use of resources and reducing waste associated with premature equipment disposal.
The integration of IoT technologies with AI further enhances the capabilities of predictive maintenance systems, enabling real-time monitoring and analysis across entire factories. This holistic view not only helps in maintenance but also assists in optimizing manufacturing processes and improving safety standards, thus reinforcing Japan’s position as a leader in industrial innovation and smart manufacturing.
The Rise of Predictive Maintenance AI in Japan
Cost Savings Through Reduced Downtime
- The implementation of predictive maintenance AI allows Japanese manufacturers to minimize unplanned downtime by anticipating equipment failures before they occur. By repairing or replacing parts based on AI-generated predictions, companies can service machinery during planned maintenance intervals, avoiding interruptions to production. This proactive approach reduces waste and leads to substantial cost savings, with some manufacturers reporting up to 25% lower maintenance costs.
Maximizing Productivity and Efficiency
- With AI monitoring equipment around the clock, any deviations from normal operating parameters are detected immediately, allowing issues to be addressed promptly. This helps ensure machinery is performing optimally at all times, enhancing productivity and overall efficiency. AI-enabled predictive maintenance is particularly impactful for Japanese manufacturers that operate complex equipment or tightly controlled production processes where any interruptions can severely hamper output.
Supporting Environmental Sustainability Goals
- The predictive capabilities of AI also support Japan’s environmental objectives by helping companies optimize resource usage and reduce waste. Parts can be replaced or repaired precisely when needed rather than prematurely, extending the usable lifespan of machinery and components. This environmentally-friendly approach to maintenance dovetails with Japan’s commitment to sustainable manufacturing and a circular economy. Overall, predictive maintenance AI is revolutionizing factory operations in Japan’s manufacturing sector. By minimizing downtime, maximizing efficiency, and enabling sustainable resource usage, this technology has become indispensable for globally competitive Japanese manufacturers. With further advancements in AI and IoT, predictive maintenance will only become more sophisticated, ushering in a new era of intelligent and hyper-efficient smart factories.
How Manufacturers Are Using AI to Predict Equipment Failures
Manufacturers are embedding sensors in machinery that gather data on metrics like vibration, temperature, and pressure. AI systems analyze this data to detect patterns that indicate impending equipment failures. Predictive Models and Algorithms
AI algorithms are trained on large datasets of historical sensor and maintenance data to build predictive models that can forecast breakdowns. These algorithms look for anomalies in sensor data that deviate from normal operating parameters. By identifying these anomalies early, the AI can predict when a failure is likely to occur, allowing maintenance to be scheduled proactively.
Reduced Downtime and Cost Savings
- Predictive maintenance minimizes unexpected downtime, enabling a seamless production flow. It also decreases costs associated with emergency repairs and overtime pay for technicians. With longer intervals between repairs, fewer spare parts are needed, and equipment lifetimes are extended. According to Hitachi, their predictive maintenance system has cut unplanned downtime by up to 50% for some manufacturing clients.
Enhanced Productivity and Sustainability
- When machinery is running at optimal performance, overall productivity increases. Predictive maintenance also supports sustainability goals by optimizing resource usage and reducing waste from premature equipment disposal or over-maintenance.
The Future of Smart Factories
- Integrating predictive maintenance with IoT technologies enables real-time monitoring and analysis of entire factories. This provides a holistic view that can further optimize processes, improve safety standards, and strengthen Japan’s position as a leader in smart manufacturing. AI will be pivotal in the development of autonomous factories that self-diagnose and self-optimize to revolutionize the industry.
The Benefits of Predictive Maintenance for Japan’s Factories
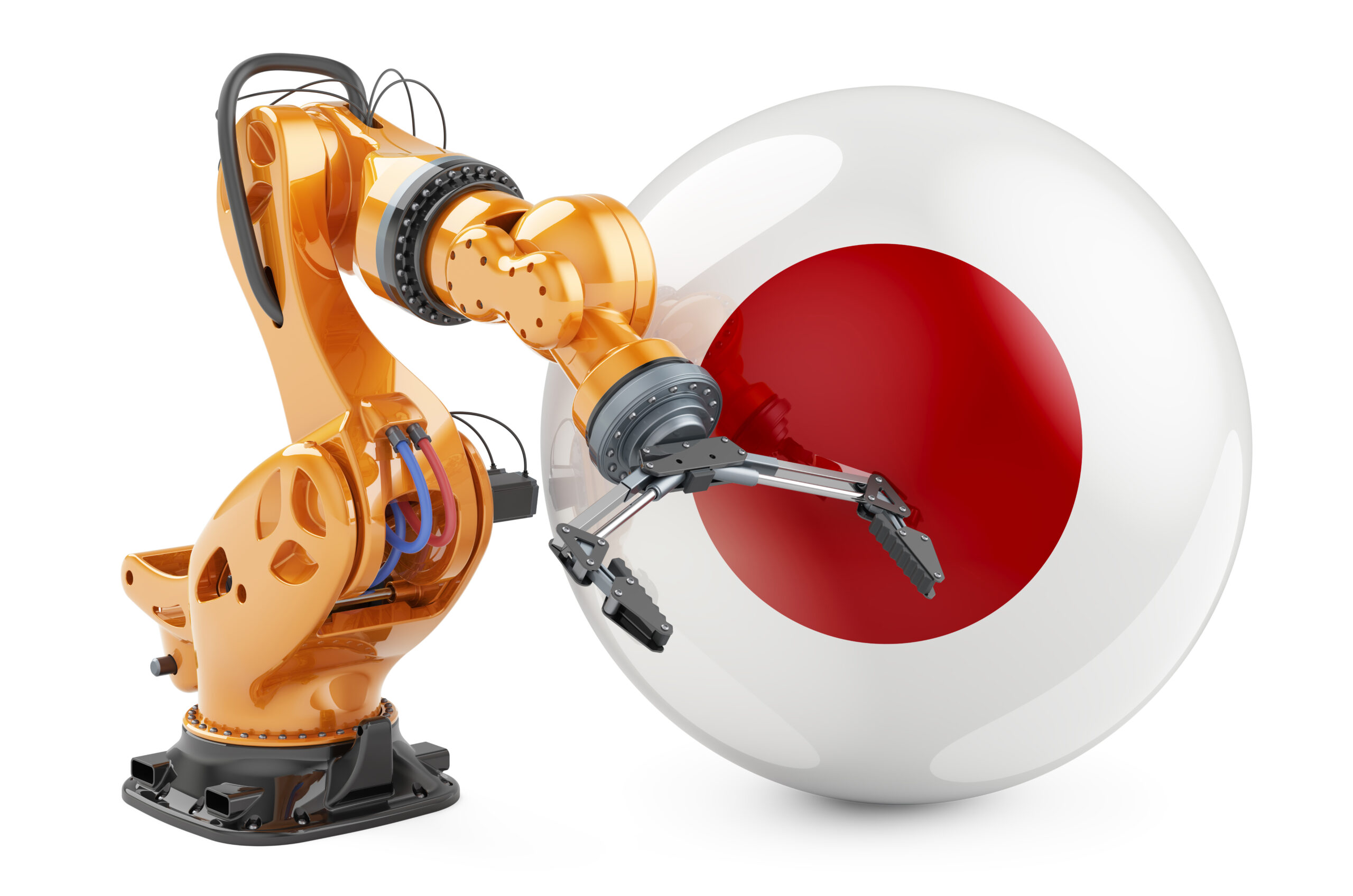
Reduced Costs
- The implementation of predictive maintenance systems leveraging AI and IoT technologies allows Japanese factories to minimize unplanned downtime and extend the lifespan of equipment. By predicting failures before they occur, companies can schedule maintenance efficiently and source necessary parts in advance. This results in substantial cost savings through the reduction of emergency repairs and premature equipment replacement.
Optimized Productivity
- With an advanced warning system monitoring equipment in real-time, factories can ensure machinery operates at maximum efficiency. Predictive algorithms provide alerts in advance of potential issues, allowing time for preventative maintenance to be performed during standard servicing periods. This minimizes unexpected interruptions, enhancing overall productivity and output.
Environmental Sustainability
- The effective utilization of resources is crucial for Japan to achieve its environmental goals. Predictive maintenance supports sustainability by allowing machinery and equipment to be used for longer periods before disposal. With optimized servicing intervals and reduced waste from emergency repairs, the demand for new parts is diminished. This conserves both materials and energy that would otherwise be expended in the production and transportation of replacement components.
The integration of AI and IoT in predictive maintenance systems provides a holistic view of factory operations. This assists not only in optimizing equipment servicing but also improves process efficiency, safety monitoring, and quality control. For Japan’s advanced manufacturing sector, predictive maintenance is a key tool for gaining a competitive advantage through cost reduction, productivity gains, and environmental leadership. With substantial government and private sector investment in this technology, Japan is poised to be at the forefront of smart factory innovation.
Techniques and Technologies Enabling Predictive Maintenance
Predictive maintenance utilizes a combination of techniques and technologies to monitor equipment, analyze operational data, and predict potential failures. Sensor data is collected from machinery and fed into AI systems that detect anomalies and identify patterns indicative of decreased performance or impending breakdowns.
AI and Machine Learning
- AI algorithms analyze huge amounts of data from sensors and historical records to detect subtle changes in vibration, temperature, and other metrics that human operators would likely miss. Machine learning allows these systems to improve over time by learning from new data. As more data is gathered, the algorithms become adept at spotting failures earlier with higher accuracy.
Internet of Things (IoT)
- The IoT connects sensors and devices across a network, enabling data sharing and real-time monitoring. In a manufacturing context, this means that sensor data from machinery across an entire factory can be aggregated and analyzed holistically. This provides a comprehensive view of operations and equipment health, allowing for predictive maintenance at scale.
Anomaly Detection
- AI systems can establish a baseline of normal operating parameters for machinery by analyzing data over time. Once a baseline is set, the system monitors incoming data for deviations, known as anomalies. Minor anomalies may indicate decreased performance, while major anomalies often point to impending failures. The key is detecting these changes early enough to schedule proactive maintenance.
Root Cause Analysis
- In some cases, AI may not only predict that a failure is likely to occur but also determine the underlying cause. By analyzing relationships between multiple data points, the system can isolate the root cause of decreased performance or other issues. This allows maintenance teams to address problems at their source, improving long-term equipment health and efficiency.
The integration of these technologies is enabling a new paradigm of data-driven, proactive maintenance. Predictive maintenance stands to revolutionize manufacturing by maximizing productivity through optimized equipment performance and minimal unplanned downtime. With the support of AI and IoT, Japanese manufacturers are poised to lead the way.
Predictive Maintenance AI FAQs: Your Top Questions Answered
1. What is predictive maintenance AI?
Predictive maintenance AI refers to artificial intelligence systems that analyze data from sensors in machinery to predict equipment failures before they occur. Advanced algorithms detect patterns in operational data that indicate impending breakdowns, allowing companies to perform maintenance at optimal times.
2. How does predictive maintenance AI work?
AI systems rely on machine learning, a field of AI where algorithms detect complex patterns in large data sets. The AI is first trained on data from properly functioning equipment, learning the normal operating parameters. The AI then monitors real-time data from machinery sensors, identifying anomalies that indicate potential failures so maintenance can be performed pre-emptively.
3. What are the benefits of predictive maintenance AI?
The key benefits of predictive maintenance AI are:
- Cost savings from reduced unplanned downtime and fewer emergency repairs.
- Improved production efficiency by maximizing uptime and performance.
- Extended equipment lifespan through optimized maintenance scheduling.
- Enhanced safety and compliance by identifying issues before catastrophic failures.
- Reduced environmental impact by decreasing waste from premature equipment replacement.
4. What types of data are used for predictive maintenance AI?
The AI requires data from sensors embedded in machinery, such as:
- Vibration data which detects changes indicating wear or damage.
- Temperature data to identify overheating components.
- Pressure data to monitor changes in fluid levels or detect blockages.
- Acoustic data to identify new or louder noises indicating potential faults.
- Visual data from cameras detecting physical damage or changes in operations.
5. What is the future of predictive maintenance AI?
Predictive maintenance AI is transforming manufacturing by moving from reactive to pre-emptive maintenance. Integrating predictive maintenance with other technologies like IoT and robotics will enable fully autonomous maintenance systems, maximize productivity, and revolutionize the factory of the future. AI’s potential to enhance efficiency, reduce waste, and improve safety makes it a vital tool for sustainable and ethical manufacturing.
To Keep It Short
In summary, predictive maintenance AI is transforming manufacturing in Japan. By leveraging advanced algorithms to analyze sensor data and identify potential equipment failures before they occur, this technology is delivering immense value through cost savings, improved efficiency, reduced waste, and enhanced optimization across factory operations. As Japanese manufacturers continue to innovate in this field, integrating AI with industrial IoT for even greater capabilities, the nation solidifies its reputation as a global leader in smart manufacturing and industrial innovation. Adopting these leading-edge technologies proactively will be key for manufacturers worldwide to remain competitive in the future.
More Stories
Snapchat Brings Messaging Power to the Apple Watch
In an era where connectivity is king, Snapchat takes a pioneering leap by bringing its dynamic messaging capabilities to the...
Apple Unlocks Its AI: Developers Get a Passport to On‑Device Intelligence
At WWDC 2025, Apple has unveiled a transformative shift in its approach to artificial intelligence, offering developers unprecedented access to its on-device AI models through the innovative Apple Intelligence framework.
Microsoft Elevates AI Shopping with Safety-First Model Rankings
With the introduction of a safety-first metric to its Azure Foundry model leaderboard, Microsoft empowers cloud customers to make more informed decisions.
Samsung’s AI Power Play: Perplexity Partnership Signals Shift from Google
Samsung is poised to redefine AI in its Galaxy smartphones through a bold strategic move. It has partnered with Perplexity AI, an innovative U.S.-based startup. This signals a possible shift away from Google’s AI ecosystem. As a result, Samsung may integrate Perplexity’s advanced assistant into its devices.
DeepSeek R1-0528 Powers Open-Source AI Challenge to OpenAI and Google
In the fast-changing world of artificial intelligence, DeepSeek's new model, DeepSeek-R1-0528, stands out as a strong competitor. It challenges major...
ChatGPT Deep Research Now Integrates with Dropbox and Box for Enhanced Data Access
ChatGPT Deep Research integration with Dropbox and Box enhances data access for users enabling them to link cloud storage accounts directly to Deep Research.